27.12MHz
RF Technology and Advantages
Quick Defrosting
Conventional defrosting:
◆ The selection, implementation and monitoring of freezing and defrosting methods are essential for the quality control of raw materials and finished products. Conventional defrosting methods cause many problems directly related to heat transfer phenomena;
◆ Heat transfer is inherently a slow mechanism, the larger the size of the product, the longer the defrosting process takes, resulting in a long time delay between taking the product out of the cold storage and processing it;
◆ Because bacteria can survive at sub-zero storage temperatures, a large number of bacteria grow and multiply in the product during the slow and warm and humid defrosting process;
◆ Longer defrosting time will lead to higher drip loss (5%~8%), resulting in changes in product texture and major economic losses;
◆ It is not possible to accelerate the defrosting process by increasing the temperature, as this may lead to serious deterioration of the product surface;
◆ Long defrosting time means that batch handling cannot be avoided, resulting in high processing costs and increasing the risk of damage to other products such as breakage and bruising;
◆ Since the heat required for defrosting is provided by air, water or steam in the processing room or in equipment with a large contact surface with the environment, the processing speed is often affected by external environmental conditions that are difficult to control.
RF defrosting:
◆ Because radio frequency (RF) electromagnetic fields can quickly generate heat inside the product, the disadvantages of traditional defrosting methods can be avoided. The heating process is fast, uniform and controlled, which significantly reduces drip losses and minimizes product deterioration caused by bacterial multiplication. The RF heating mechanism provides flexibility for production scheduling and is the ideal solution for many heating, softening and defrosting processes.
◆ The product is placed on the conveyor belt of the machine through the RF box (between the upper and lower electrode plates). When the RF generator applies a high frequency alternating voltage between the electrodes, the water molecules at the two poles of the frozen product vibrate and rotate in order to adjust themselves to the polarity of the rapidly changing opposite electrode, which causes friction between the molecules, resulting in rapid and uniform heat generation throughout the product (regardless of product size, weight, shape and thermal conductivity).
◆ The amount of heat generated inside the product and the defrosting time can be precisely controlled by adjusting the voltage applied on the electrode plate and the speed of the conveyor belt.
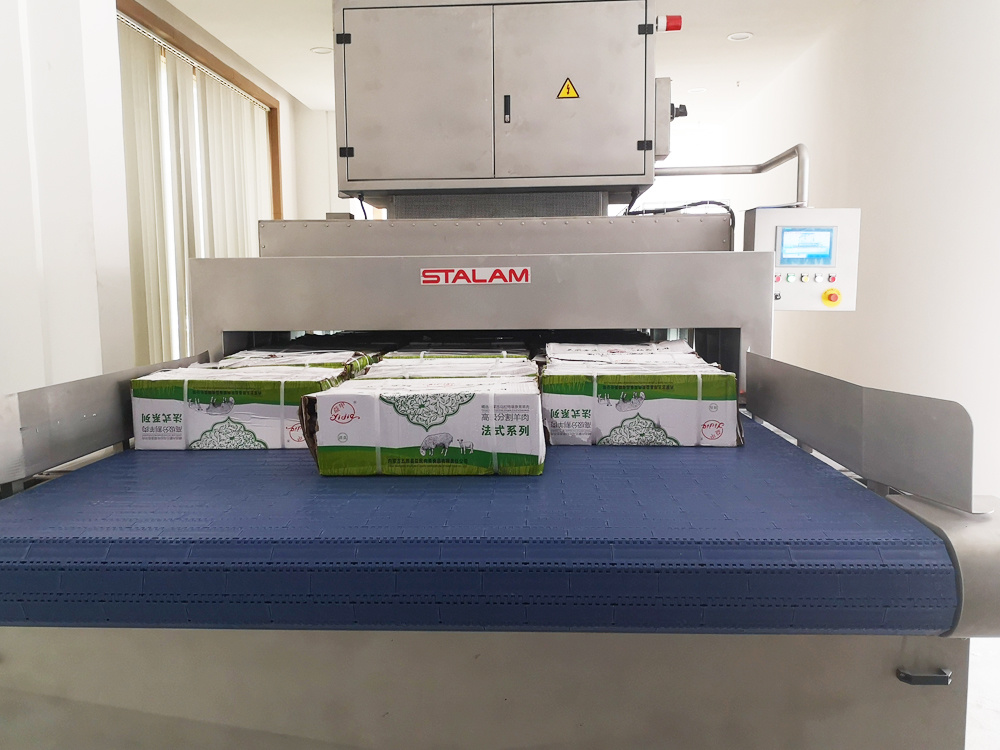
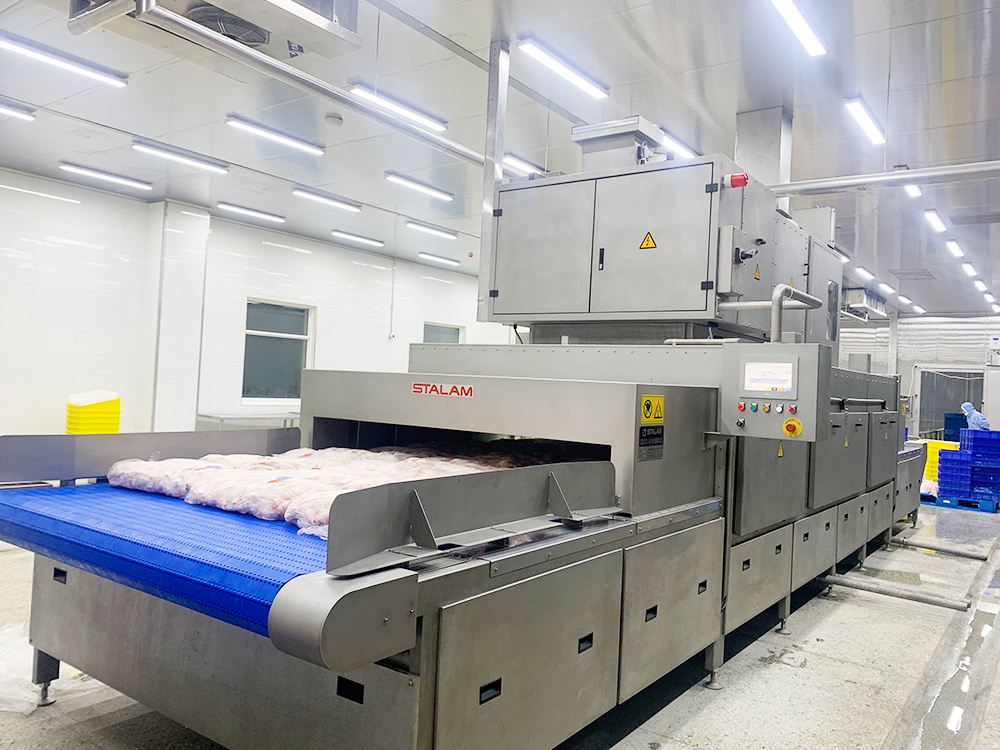
Advantages:
◆ Defrosting in short time
Defrosting takes minutes instead of hours/days (even if the product is large). If necessary, it can be defrosted directly in the packaging used for storage or retail (cardboard boxes, polyethylene bags, etc.).
◆ No drip, no product degradation
The speed and uniformity of the treatment minimizes the risk of product deterioration: no drip loss, no sensory, physical or chemical changes, no bacterial growth. Thus preserving the best quality of the product.
◆ Higher yield
There is almost no drip loss, which means that the weight loss (up to 6-8%) caused by traditional defrosting methods is completely eliminated. The increased output brings direct economic benefits, making the payback period of RF equipment as short as 6 to 12 months.
◆ Uniform and controlled processing
The product can accurately reach the temperature required for the next process. In addition, weather and external environmental conditions do not affect defrosting, so it can be controlled accurately and consistently.
◆ Small footprint, lower process cost
Rf equipment requires a much smaller footprint than traditional large defrosting repositories or equipment; Since there is no energy loss to the environment, the defrosting energy consumption is also greatly reduced.
◆ Flexible production
Due to the fast and continuous processing speed, RF defrosting has significant advantages in product handling and production scheduling. Production can be organized according to the "zero inventory" standard - a great benefit in cases where new orders are added temporarily, or orders in process are changed at the last minute.
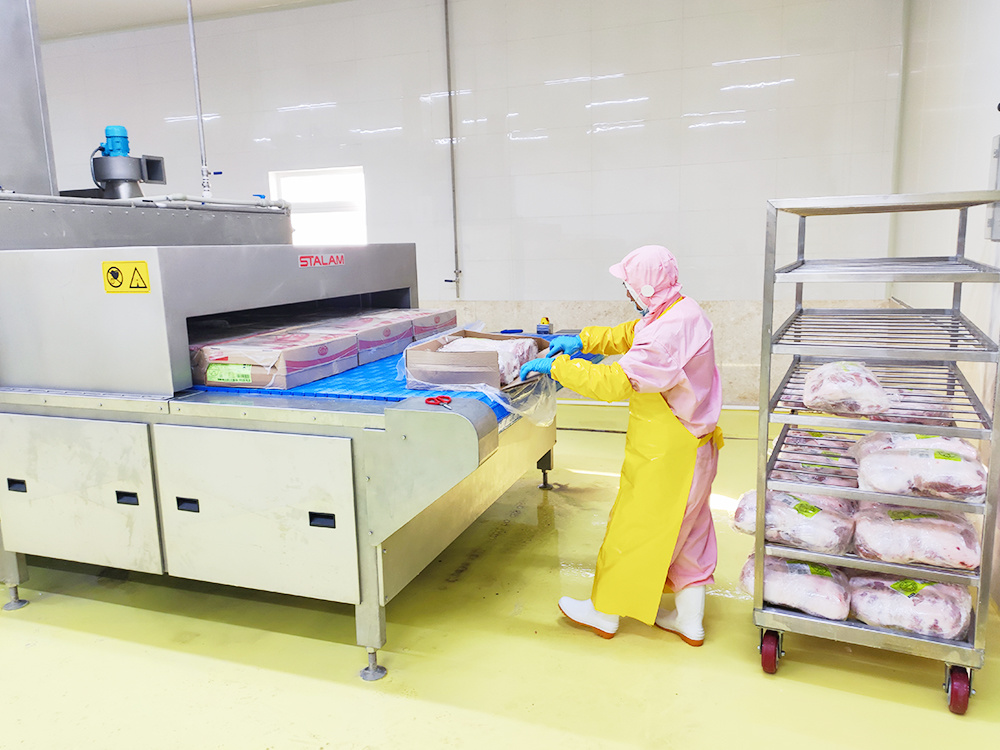
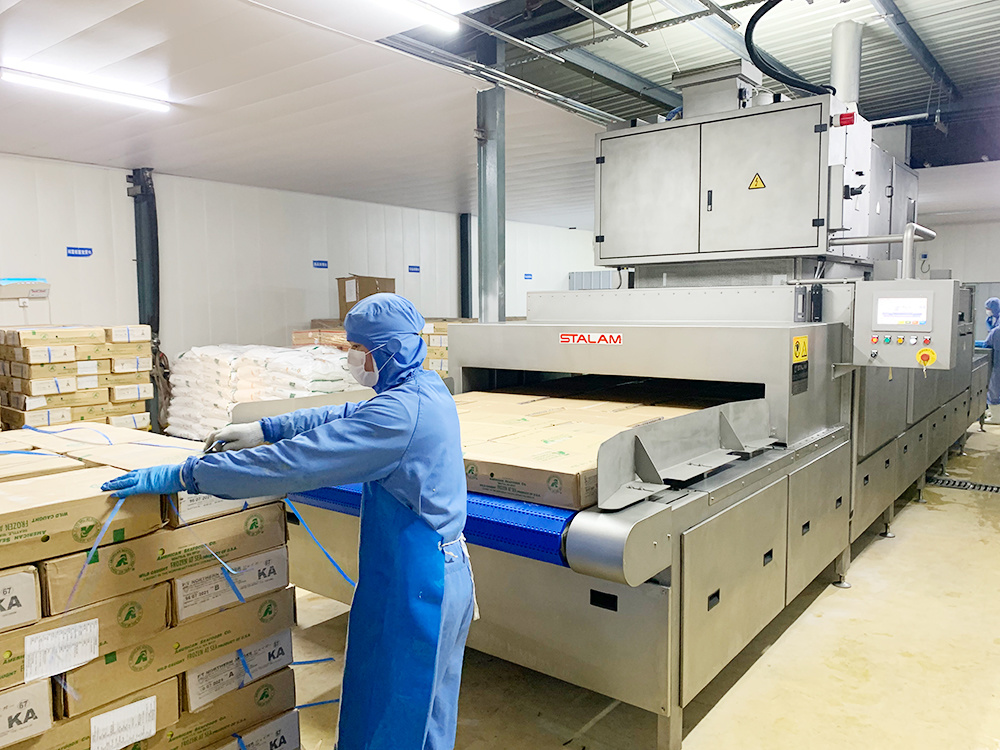
Features of RF defrosting equipment:
◆ RF working frequency: 27.12MHz
◆ SUS304 stainless steel structure treated by anti-corrosion (passivation, pickling) and sandblasting.
◆ Protection level: IP65. The external protection box of the RF generator is made of SUS304 stainless steel plate.
◆ Wide conveyor belts (up to 180cm wide) are made of certified food-grade rigid polypropylene modules (for packaged products) or hardened polyester surfaces (for unpackaged products).
◆ Built-in conveyor belt and processing bin cleaning system, through a number of side doors for a comprehensive cleaning of the machine inside.
◆ Can be used for a variety of products defrosting process formula PLC control system.
◆Modular structure: The specification of STALAM RF defrosting machine is 7KW/40KW/85KW/170KW. Can be connected in series to increase production. If production is increased, additional RF modules can easily be used in series with already used defrosting equipment.

No. 98, Lane 4788, Bao 'an Highway, Anting Town, Jiading District, Shanghai
Copyright of the page: Shanghai Deyi Machinery Manufacturing Co., Ltd www.300.cn SEO Privacy Policy