27.12MHz
RF Technology and Advantages
RF VS Microwave
Radio frequency (RF) and microwave (MW) are both "endogenous" heating methods. This means that the heat source is not slowly transferred from the outside through its surface to the inside of the product, as is the case with conventional heating methods based on heat conduction, convection and radiation, but is directly generated throughout the product, thanks to the energy of the electromagnetic field being converted into heat energy by oscillating at the appropriate frequency.
Although the heating mechanisms of RF and microwave are similar and equally effective in some applications, there are some fundamental differences between the two technologies; The unique characteristics of RF technology and RF equipment make this technology often the best choice and sometimes the only solution for a variety of industrial production processes.
◆ Higher penetration depth
Due to its short wavelength and poor heating permeability, the industrial use of microwaves is limited to applications on relatively small products. In contrast, radio frequency, due to its longer wavelength and the resulting ability to penetrate deeply into dense and large-sized materials, allows it to be widely used in products of almost any size.
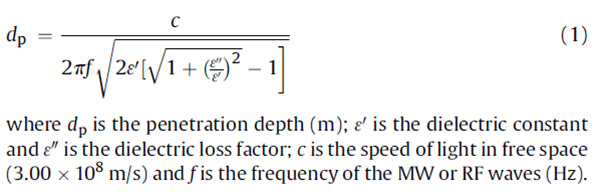
dp: heating penetration depth (m);
E ': dielectric constant;
E ": dielectric loss factor;
C: The speed of light in free space (3×108m/s);
f: Frequency (Hz)
◆ Better heating uniformity
The energy transfer from the microwave source to the product through the waveguide is a process that cannot be accurately controlled, and the microwave energy is projected from the projection point, in a fan, jet radiation to the product, so that the energy distribution in the defrosting chamber is ununiform, resulting in ununiform product temperature after defrosting. On the contrary, the projection method of the RF generator energy is uniformly transmitted vertically between the electrodes, and the energy distribution between the plate electrodes is uniform, so that the energy is uniformly projected onto the product, and the product temperature is uniform after defrosting.
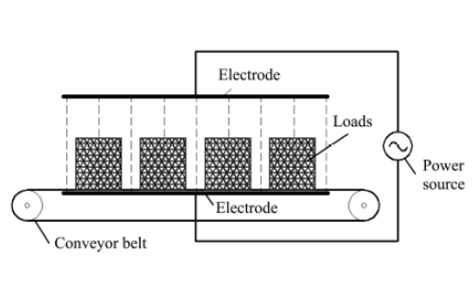
Radio frequency (RF) energy application mode
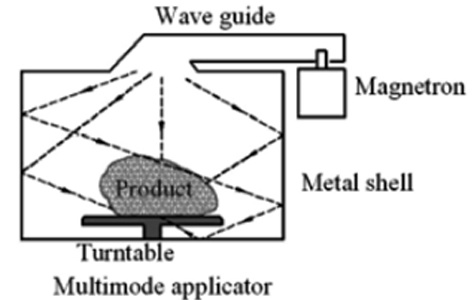
Microwave (MW) energy application mode
◆ Higher selectivity
At higher frequencies (typical microwave 915MHz/2450MHz), the difference between the loss factors of various products is usually much smaller than the difference between the loss factors at lower frequencies (typical RF 27.12MHz). This means that RF is more selective in heating products with different chemical, physical, and morphological properties (mainly heating water molecules), making it easier to control the heat treatment of different materials. This feature is very useful in drying applications, where the energy of the RF can be preferentially absorbed by the water contained in the product, allowing for fast and efficient drying without affecting the substrate.
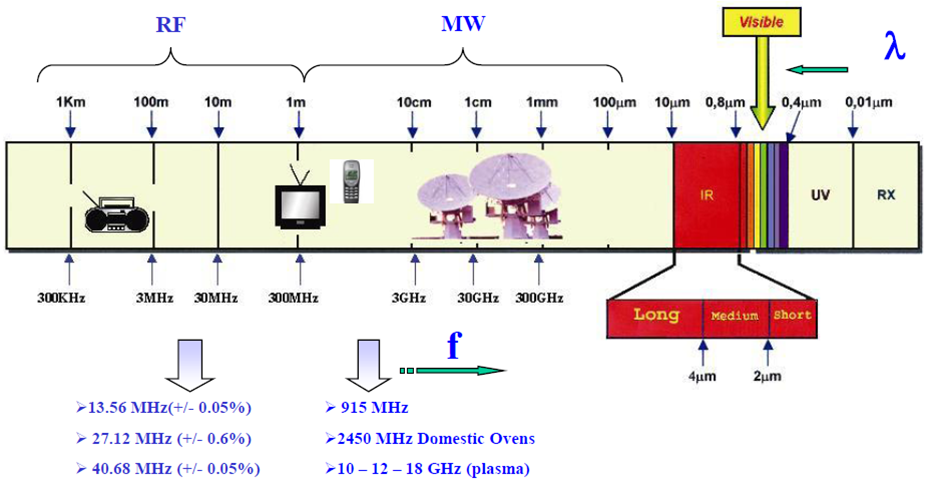
◆ Higher power generator
RF generators for industrial applications can provide a single power output value of more than 100KW. Usually, one or two RF generators are sufficient to meet the heat treatment or drying capacity required for production lines in different industrial sectors.
In contrast, magnetrons used to generate microwaves, except for the 915 MHz technology, can only provide unit power values within a few KW (typically about 1 to 3 kW at 2450 MHz). To cope with the power values required for large-scale industrial production, installing and controlling dozens or even hundreds of magnetrons is technically complex and expensive, with a higher failure rate.
◆ Easier power regulation and higher operation flexibility
RF energy is "on-demand absorption" of the product, rather than "forced" onto the product; By simply adjusting the working parameters of the machine, the energy absorbed by the product can be accurately controlled according to the process requirements, regardless of the amount of product submitted to the process. In addition, in drying applications, the output power of RF is actually self-regulating, in the sense that the higher the moisture content, the higher the energy absorbed, and vice versa. As a result, moisture inhomogeneity within the product is automatically reduced, reducing the risk of over-drying or overheating.
Instead, the magnetron is a "generator" driven by a PLC that forces output according to a set power value, and cannot accumulate in empty space, so it must be forced and fully absorbed by any number of products placed there. This is why it is difficult to accurately control the heating or drying process by microwave: the number of products being treated must always be known so that the thermal effect that needs to be generated can be determined, and the energy to be transferred must be constantly adjusted (as product specifications change).
◆ Higher energy efficiency
Although the energy efficiency of RF and microwave generators is comparable (about 70%), the operating mode and energy reflection phenomenon of microwave devices make their overall energy efficiency only about 55%.
Therefore, compared with the corresponding microwave equipment, the energy efficiency of the RF equipment is about 10-15% higher, in other words, the use of RF equipment will save about 10-15% of energy consumption.
◆ Reduce investment and maintenance costs
Due to the large-scale industrial production of magnetrons and their electronic control components, home microwave ovens are competitive on price. Industrial equipment is a different story: the price of RF equipment has become extremely competitive with microwave equipment, thanks to RF high-power generators and their simple electronic controls. In addition, in terms of maintenance costs, post-RF maintenance is significantly more convenient and cheaper due to the reduction in the number of "core" components that need to be replaced regularly (one or two triode after about 15,000 working hours versus tens or even hundreds of magnetrons after about 5,000 working hours).
◆ Safer operation
Microwave with short wavelength is particularly "aggressive" and difficult to block. A variety of techniques and engineering solutions are required to carefully manufacture and safely operate industrial microwave equipment. In developed countries, for safety reasons, microwave machines must be installed with a microwave leak detector connected to the generator (once the radiation leakage exceeds the standard, the generator will stop working immediately).
In contrast, radio frequency has longer wavelength, which makes them less aggressive and easier to shield, easily reaching the leakage levels accepted by international standards. In particular, even with generators of 100 kW or larger operation at full power, open processing tunnels can be used without any safety problem.
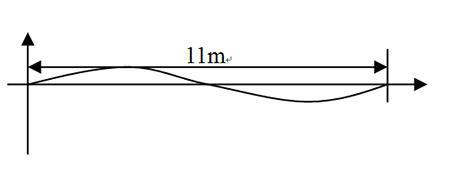
Radio frequency (RF 27.12MHz) waveform diagram
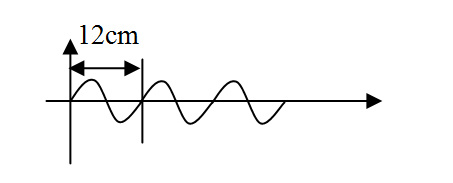
Microwave (MW 2450MHz) waveform diagram
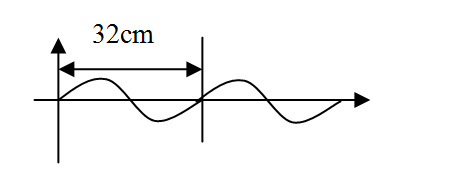
Microwave (MW 915MHz) waveform diagram

No. 98, Lane 4788, Bao 'an Highway, Anting Town, Jiading District, Shanghai
Copyright of the page: Shanghai Deyi Machinery Manufacturing Co., Ltd www.300.cn SEO Privacy Policy